Table of Contents Show
In the world of industrial machinery, unexpected downtime can be a huge drain on resources. High costs, interrupted workflows, and reduced productivity are just a few of the potential pitfalls. One might be tempted to take shortcuts during the servicing process of these heavy-duty machines in an attempt to save time or money. Unfortunately, such practices can ultimately lead to equipment failure and diminished operations. To make matters worse, you could find yourself faced with expensive repair bills.
In this article, we delve deeper into some common missteps you may be making when maintaining your industrial equipment. We also provide practical advice on how to sidestep these issues, ensuring your machinery operates at peak performance.
1. Overlooking the Specific Maintenance Required

Every piece of surplus industrial equipment is distinct, with its own set of maintenance needs. Disregarding these unique requirements can lead to significant complications and disruptions in your operations. To prevent such scenarios, each company must formulate a bespoke maintenance strategy that caters to the specific needs of all their machinery. This comprehensive plan should encompass:
- Routine Maintenance: Schedule regular upkeep activities at certain intervals to ensure the machines are kept in optimal working condition. This could include tasks such as lubricating moving parts, replacing worn-out components, or tightening loose bolts.
- Prompt Repairs and Replacements: When a component becomes faulty, it’s imperative to repair or replace it promptly. Delaying these repairs can compound the problem, potentially leading to complete machine failure.
- Regular Inspections: Regularly monitor the health of your machines through inspections. This practice will help you identify potential issues before they escalate into major problems.
Underestimating the significance of machine-specific maintenance could result in considerable expenses in the future. It’s not just about preventing breakdowns – but also about extending the lifespan of your equipment and ensuring its reliability. It’s therefore essential for businesses to invest time and resources into well-thought-out maintenance plans that cater explicitly to each machine under their care.
Remember: “An ounce of prevention is worth a pound of cure.” – Benjamin Franklin
By being proactive in your approach towards maintaining your industrial machinery, you’re not only saving money down the line but also improving overall productivity and operational efficiency.
Also Read: Heavy Machinery Rental: Top Myths About Used Heavy Machinery
2. Neglecting Parts and Tool Repairs
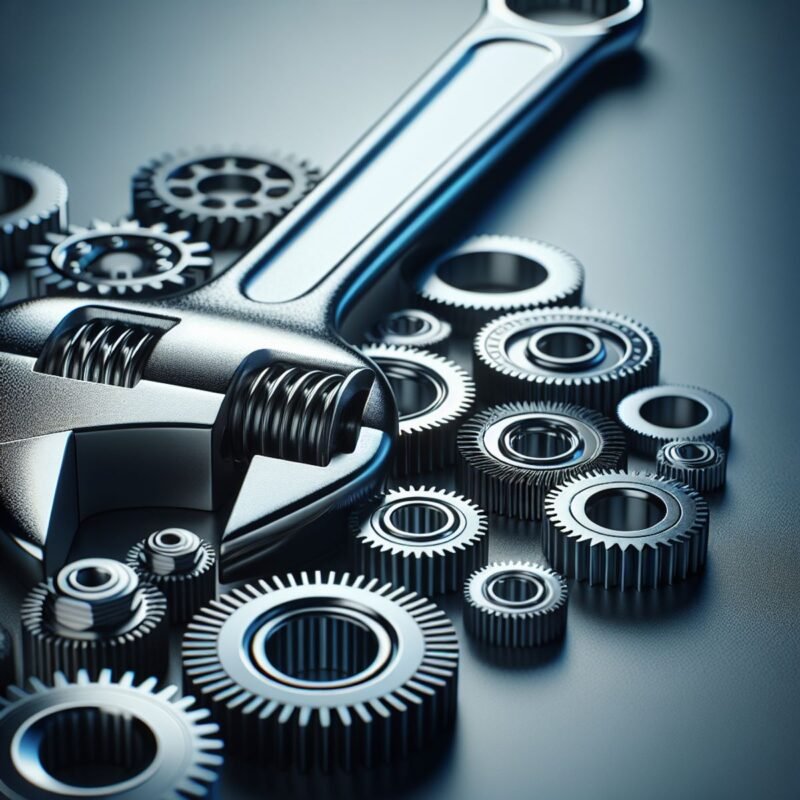
Maintaining industrial machinery is no small feat. It demands both the use of high-quality parts and tools, as well as their optimal upkeep through regular cleaning and checks. Yet, in many workplaces, this crucial aspect of industrial maintenance is often neglected.
The reasons behind this neglect can vary. Given the high cost attached to these specialized parts and tools, some companies may hesitate to invest in necessary repairs or replacements. Additionally, the difficulty associated with replacing these components might deter some from addressing issues promptly.
However, it’s essential to remember that neglecting repairs or replacements to save on short-term costs could lead to larger expenses in the long term. The following points emphasize why it’s crucial not to skimp on repairs:
- Early Failure of Equipment: Ignoring minor issues can lead to early equipment failure. Smaller problems can gradually worsen over time, causing severe damage that could have been prevented with timely repair.
- Decreased Productivity: Faulty parts can slow down machine operation, leading to decreased production rates and overall productivity.
- Safety Hazards: Damaged tools or parts can potentially pose safety risks for operators. Regular maintenance ensures a safer working environment.
“A stitch in time saves nine.”
This old adage perfectly encapsulates the importance of prompt repairs in industrial settings. It’s not just about saving money; it’s about ensuring the efficiency, safety, and longevity of your machinery.
For more information on tool repairs, you can refer here. Remember: investing in regular maintenance and timely repairs is an investment in your business’s profitability and sustainability. Always ensure that all parts and tools used in industrial equipment maintenance are well-maintained and repaired when needed.
3. Lacking a Consistent Maintenance Routine
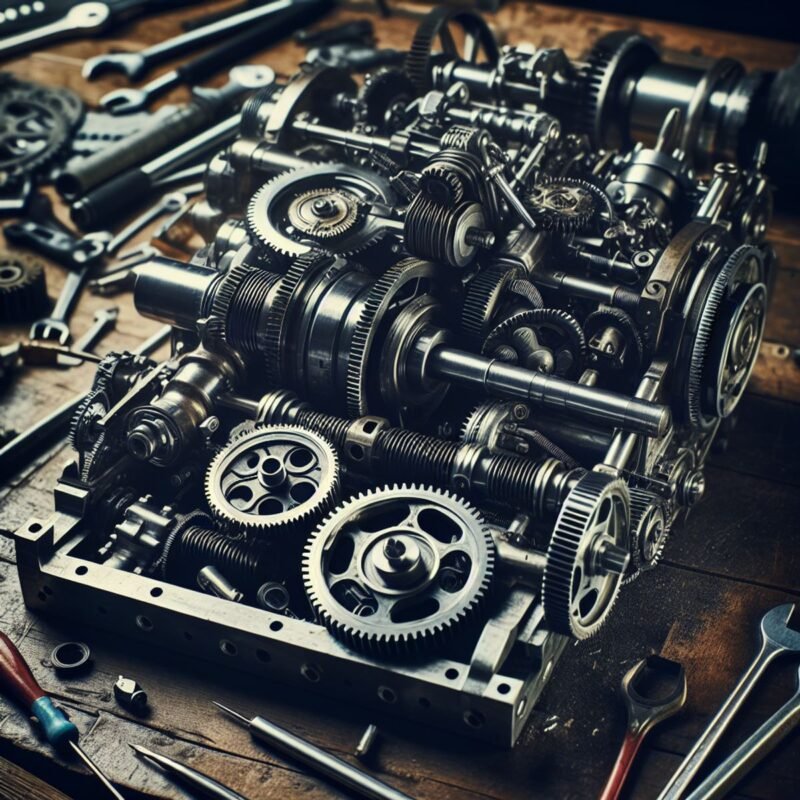
The lack of a consistent, well-structured maintenance routine is a common pitfall that can lead to undue oversight and potentially costly errors. Just as each industrial machine, such as those found in an Industrial Property For Sale, has its unique operational requirements, each should have a tailored maintenance plan to match its specific needs.
This personalized maintenance schedule should fundamentally comprise of:
- Specific tasks based on each machine’s requirements: Every machine has its own set of tasks that need to be fulfilled for optimal performance. This can range from regular oil changes to complex part replacements. Understanding what each machine needs and tailoring the maintenance tasks accordingly is crucial.
- Records of service maintenance for future reference: Keeping track of past services aids in predicting potential issues and in planning future servicing schedules. These records can be extremely helpful when diagnosing issues or when you need to provide service history during tool resale or audits.
- Plans for anticipated repairs: Proactive planning is key in industrial maintenance. Predictive maintenance techniques can help anticipate potential problems before they escalate into major failures. This insight allows managers to schedule repairs during non-peak times, minimizing disruptions.
By implementing a meticulously planned and strictly adhered-to routine, potential issues can be swiftly identified and effectively addressed. This not only prevents expensive system failures but also enhances the overall lifespan and efficiency of your machinery.
Remember: “Prevention is better than cure.” A well-planned maintenance routine acts as the first line of defence against unexpected breakdowns and costly repairs.
4. Overlooking Technicians’ Feedback: A Common Pitfall
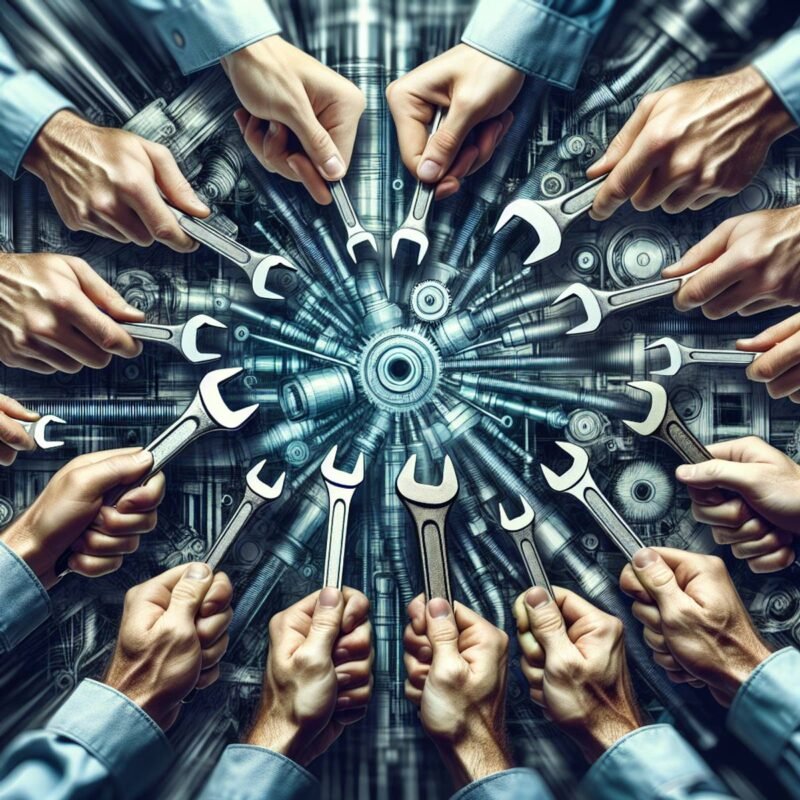
One of the common mistakes in machinery management is overlooking the invaluable feedback from technicians. As the ones who work directly with your machinery, they possess a deep understanding of its performance, potential issues, and maintenance needs.
Technicians: The Front Liners in Predicting Potential Issues
Trained technicians interact with your machinery on a daily basis. Their hands-on experience allows them to detect subtle changes or anomalies that might indicate future problems. By sharing their observations and insights, they can help you proactively address potential problems before they escalate into costly repairs.
“The technician’s eye often catches what the manager’s eye misses.”
Their recommendations regarding preventative measures are instrumental in minimizing downtime and maximizing productivity. Ignoring this valuable resource can lead to undetected issues that can eventually cause significant operational disruptions.
The Importance of Listening to Technicians’ Feedback
As facility managers, it’s more than just acknowledging the feedback; it’s about understanding its value and taking action. Implementing their suggestions not only validates their expertise but also fosters a more reliable industrial environment.
Here are a few ways to effectively utilize technician feedback:
- Incorporate regular feedback sessions: Establish a system for technicians to share their observations and recommendations regularly. This can be through weekly meetings, written reports, or digital communication platforms.
- Act on the feedback promptly: Once feedback has been provided, ensure that necessary actions are taken swiftly. This could be implementing suggested preventative measures or addressing identified issues.
- Foster open communication: Encourage technicians to voice out their observations and concerns freely without fear of retribution. An open communication environment promotes proactive problem-solving and continuous improvement.
Collaboration: Key in Documenting Issues & Establishing Routine Maintenance
Involving technicians in documenting potential issues and establishing routine maintenance schedules is an excellent way to streamline machinery management. Their on-the-ground experience can provide useful insights into the most effective maintenance strategies and schedules.
By creating a collaborative approach to machinery management, you enhance not only the reliability of your machinery but also the overall efficiency of your operations. Remember, every voice in your team has value and can contribute to successful machinery management.
5. Disregarding Safety Rules and Regulations
Ignoring safety rules and regulations is a commonly overlooked aspect of industrial equipment maintenance.
Regular Inspections
Regular inspections are not just a formality; they play a crucial role in identifying worn or faulty parts that may need immediate replacement. Inspections should be thorough and systematic, ensuring every part of the machinery is checked and tested. The results should be accurately documented to maintain transparency and facilitate easy tracking of recurring issues.
Usage of Protective Gear
Another oft-neglected rule is the usage of protective gear. Regardless of their role or level, employees should always wear the appropriate protective gear when on the factory floor. This can range from helmets and safety glasses to high-visibility jackets and steel-toe boots.
Identification and Regulation of Hazardous Areas
Hazardous areas within your facility must be clearly marked with visible signage. They should also be regulated to ensure that only authorized personnel with adequate training are allowed access.
Making Modifications to Machinery
Modifications made to machinery should be undertaken cautiously, ensuring all safety regulations are adhered to. This means before any changes are made, a risk assessment must be conducted to identify potential hazards associated with the modification.
Staff Education on Safety Regulations
Additionally, all staff members must be thoroughly educated about the safety regulations relevant to their roles. Regular training sessions can help reinforce these rules and keep them fresh in employees’ minds.
“Safety is everyone’s responsibility, and as such, each team member should understand their role in maintaining a safe work environment.”
In essence, a conscious effort towards proper maintenance practices can save your business from unnecessary costs and inconveniences associated with common industrial equipment maintenance mistakes. Here’s a quick recap of the key points:
- Conduct regular inspections
- Ensure protective gear is always worn
- Clearly mark and regulate hazardous areas
- Make machinery modifications cautiously
- Educate all staff on relevant safety regulations
Remember, it’s not just about avoiding mistakes; it’s about creating a culture of safety and maintenance that permeates every aspect of your business operations.
Conclusion
In conclusion, avoiding common industrial equipment maintenance mistakes such as ignoring specific maintenance needs, neglecting parts and tool repairs, lacking a consistent maintenance routine, overlooking technicians’ feedback, and disregarding safety rules and regulations is crucial.
Regular inspections, usage of protective gear, adherence to safety regulations, and modifications cautiously are key aspects of sound maintenance practices. These measures not only save unnecessary costs but also prevent the inconvenience caused by equipment breakdowns.
It’s essential to keep comprehensive maintenance records, conduct daily inspections, and promptly attend to necessary repairs or replacements. Considering professional maintenance services can be a beneficial investment for your business. Proactive measures today can safeguard your industrial machinery from costly errors in the future.
FAQs (Frequently Asked Questions)
One common mistake in industrial equipment maintenance is overlooking the specific maintenance required for each piece of equipment. Every piece of industrial equipment is distinct, with its own set of maintenance needs, and it’s important not to overlook these requirements.
Another common mistake to avoid is neglecting parts and tool repairs. Maintaining industrial machinery demands attention to detail, and neglecting necessary repairs can lead to unexpected downtime and costly issues.
The lack of a consistent, well-structured maintenance routine can lead to an increased risk of breakdowns and failures. Having a consistent maintenance routine ensures that all equipment is properly cared for and reduces the likelihood of unexpected downtime.
A common pitfall in machinery management is overlooking technicians’ feedback. Technicians working directly with the equipment often have valuable insights and feedback that should not be disregarded.
Ignoring safety rules and regulations is a commonly overlooked mistake that can lead to serious accidents and injuries. Adhering to safety rules and regulations is crucial for maintaining a safe working environment.
Regular inspections are not just a formality; they play a critical role in identifying potential issues before they escalate. They help ensure that all equipment is functioning optimally and can prevent unexpected downtime.